Сегодня мы с вами обсудим жизненный цикл полимера - от рождения до ресайклинга - и то, как ученые пытаются продлить его век и прокачать свойства.
Надо сказать, мы с вами, господа, сидящие сейчас у мониторов, тратим гораздо меньше ресурсов на то, чтобы продлить свою жизнь и прокачать скиллы:)
Держу пари, многие из вас держали в руках гранулы полиэтилена. Как мы уже знаем, из реактора выходят не они, а мелкодисперсный белый порошок - это полимерный «эмбрион», который превращается в «ребенка»-гранулу в экструдере. Гранулы-дети с завода-производителя едут к переработчику, перерабатываются в изделие, которое потом мы используем. Мир жесток, и на каждой из этих стадий полимер поджидают опасности:
Для снижения этих рисков в полимеры добавляют всевозможные добавки, про них сегодня и поговорим.
Итак по типу действия добавки можно разделить на 3 большие группы:
1 группа добавок - те, что помогают смешивать разные полимеры
В прошлый раз мы с вами разобрались с тем, что люди очень хотят смешать полимеры, чтобы получить новые материалы с отличными свойствами, а вот полимеры смешиваться любят не очень)
Компатибилизаторы помогают увеличить прочность связи полимер-полимер, и дать возможность получить компаунд, который не только будет обладать свойствами всех компонентов, но и - улучшенными свойствами - за счет многократного увеличения площади раздела фаз.
В прошлой статье мы писали о том, что в несмешивающихся смесях полимеров границы раздела фаз между материалами могут выглядеть по-разному, и иногда слоистое или капельное распределение одного материала в другом играет нам на руку.
Но чаще всего это работает так: чем больше размер шариков (или слоев) одной фазы в другой, тем более стабильными они являются ( т.к. небольшое количество крупных шаров обладает меньшей площадью поверхности, чем очень большое количество маленьких шариков). А поскольку наши два полимера не нравятся друг другу, то они стремятся уменьшить поверхность соприкосновения. Чем меньше площадь поверхности, тем меньше соприкасаются две фазы. Это означает, что шары будут стремиться увеличить свои размеры. При этом чем меньше размер шаров, конечно же, тем больше площадь границы раздела фаз. А чем больше площадь поверхности раздела фаз, тем более эффективно энергия передается от одной фазы к другой, а это приводит к улучшению механических свойств.
Компатибилизаторы могут действовать по-разному: улучшать смешиваемость за счет наличия в составе сополимера, который совместим с обоими компонентами компаунда (так работает известный многим Vistamax), или химически реагировать с ними (например, привитый к полимерной цепи малеиновый англидрид реагирует амидными, эфирными или гидроксильными группами других полимеров.
2 группа: снижение риска деструкции при переработки и улучшение перерабатываемости
В жизненном цикле полимера у нас минимум 2 этапа переработки - что не мало. А если мы планируем, что материал доживет до ресайклинка, на эту группу добавок стоит обратить особое внимание.
2 группа - это:
- Антациды нейтрализуют остатки кислот-катализаторов и позволяют не только уменьшить коррозию экструдеров, но и увеличить стойкость материала к температурам и кислороду воздуха. Самый известный антацид - стеарат кальция. Так же применяют микротальцит и окиси магния или цинка.
- Стабилизаторы
Все мы знаем, что свободные радикалы или разомкнутые реакционно-активные связи в функциональных группах - первые враги устойчивости материалов к температурам. Именно в расплаве происходят такие процессы, как сокращение полимерной цепи, подшивки и прочие неприятности, которые «роняют» прочность, охрупчивают и уменьшают срок службы будущего изделия. Поэтому главный принцип термостабилизаторов - обезвредить все, что жаждет прореагировать, и сделать это можно 3 способами:
- отдать «лишний» водород ( так поступают ароматические амины и фенолы)
- «забрать» радикалы (известные акцепторы радикалов - HALS, гидроксиламины, лактоны, фураноны)
- разрушить перекисные соединения (для этого применяют гидроксиламины, фосфиты и фосфониты)
УФ-старение полимера происходит по тем же механизмам, но защитить материал можно с помощью УФ-стабилизаторов, которые имеют несколько иной принцип работы:
- Квенчеры (комплексы Ni, дибутилтиокарбонаты цинка) умеют «тушить пожар». Как мы ранее говорили, молекулы полимера не только постоянно дрыгаются, вибрируют и сдвигаются относительно друг-друга, как люди на танцплощадке, они еще и держатся за руки в своем безумном танце. Когда УФ-свет попадает на материал, он придает молекулам ускорение и стимулирует их двигаться активнее, что приводит к риску разрыва связей - как если бы танцующие слишком разошлись и расцепили руки. Квенчеры перехватывают возбуждение, переданное световой волной и гасят его до того, как материал успел разложиться.
- УФ-абсорберы поглощают световую энергию и трансформируют ее в тепловую ( так работают преимущественно бензофеноны)
- Процессинговые добавки
Смазки (они же «скользячки») улучшают не только внешний вид, но и перерабатываемость. Для этого применяют жирные кислоты (стеариновая, пальмовая), амиды жирных кислот (эрукамид, олеамид), воски, фторполимеры, полисилоксаны, стеараты металлов (помните, где еще мы о них слышали?)
Антистатики особенно ценны для тех, кто занимается пленками и видел как пленка может «стрелять» на линии. Обычно электросопротивление таких добавок составляет примерно 10Е10-Е12 Ом. В качестве антистатиков применяют или фосфаты низкомолекулярных кислот или четвертичные аммонийные соли.
3 группа - самая многочисленная - добавки, модифицирующие свойства материала и изготовленного из него изделия.
Их можно условно разделить на 2 группы по принадлежности к классам химии - на минеральные (неорганические) и органические - и на 50+ групп по фактору, на который они влияют. Так что остановимся на первой классификации.
Минеральные (неорганические) наполнители могут быть:
- волокнистыми - это стекловолокно, углеволокно, базальтовое волокно - чаще всего применяются как армирующие добавки, снижающие линейное тепловое расширение.
Надеюсь, никто из вас никогда не столкнется с такой ситуацией:
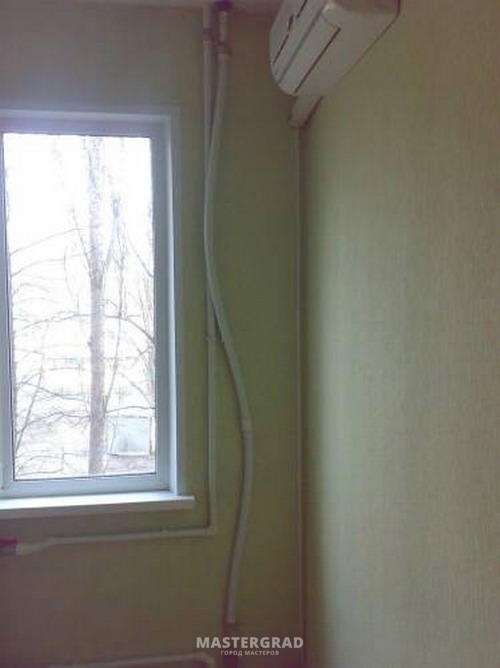
Поверьте - это не замысел дизайнера. Это термическое расширение полипропиленовой трубы, по которой течет горячая вода, и как следствие - ее деформация. Трубы, средний слой которых армирован 10-20% волокна, расширяются в 5-10 раз меньше.
Армирование полимера минеральными волокнами так же распространено в сфере конструкционных пластиков типа полиамида, из которых изготавливают фурнитуру и детали сложных механизмов - таких, которым следует не только сохранять размеры во всем диапазоне эксплуатационных температур, но и быть прочными и стойкими к абразивному износу.
- ткаными и неткаными - широко распространены в сфере производства геосинтетических мембран
- порошковыми - мел, тальк, каолин, бентониты, древесная мука, стеклошарики, гидроксиды, диоксид кремния и т.д..
Не смотря на то, что мел получил широкую популярность как средство увеличения плотности полимерной продукции (а значит и маржинальности) и часто считается нежелательным компонентом в любых компаундах, надо отдать ему должное - введение адекватных количеств мела повышает прочность и жесткость материала, в некоторых случаях - способствует улучшению свариваемости, а тот факт, что на рынке часто реализуется мел, обработанный стеариновой кислотой, делает его еще частично компатибилизатором, частично - антацидом ( см. выше).
Гидроксиды зачастую применяются как ингибиторы распространения пламени - антипирены (поговорим о них чуть позже).
Бентониты за счет гигроскопичности и большой площади поверхности легко подвергаются обработке всевозможными ПАВами, аммонийными солями, и могут использоваться как носители других полезных добавок. А кроме того, силикаты имеют слоистую структуру, попадая в расплав полимера, распадаются на наноразмерные чешуйки и создают в компаунде своеобразный каркас, увеличивая прочность и жесткость.
Тальк и диоксид кремния используются как антиблоки - то есть добавки, которые снижают слипаемость поверхностей за счет создания на поверхности дополнительной шероховатости:
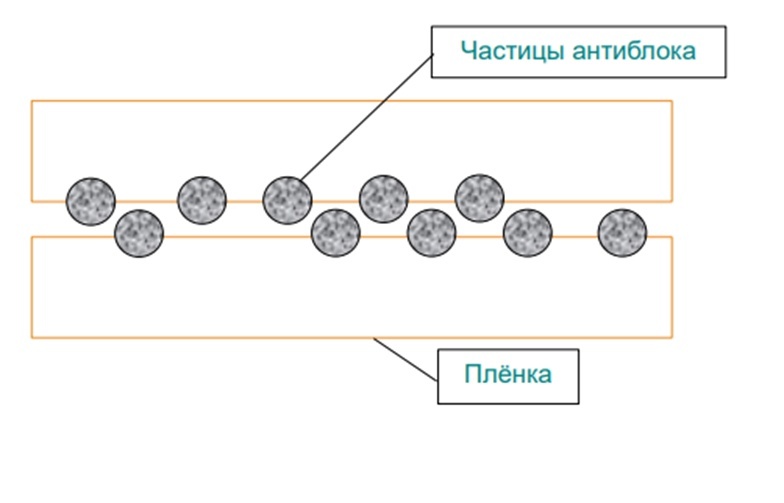
Органические или смесевые добавки -
это:
I. Добавки, работающие с внешним видом и поверхностью (трением):
- Красители и пигменты
- Антифоги - снижают запотевание пленки и позволяют нам с вами, вытащив из морозильной камеры упаковку с морским окунем, разглядеть внутри нее не только очертания плавников, но и даже выражение глаз несчастной и вкусной рыбины. В качестве антифогов применяют: эфиры и полиэфиры глицерина, эфиры и этоксилированные соедиенения сорбитана, этоксилаты спиртов и нонил-фенола
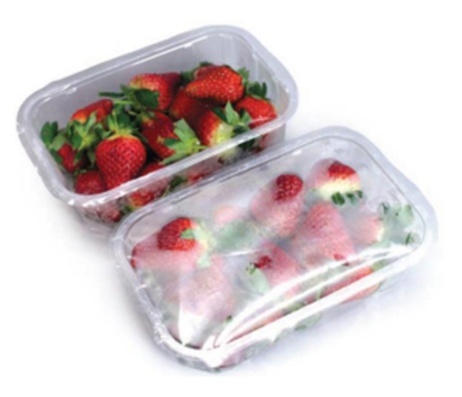
3.«Скользячки» -мы о них упоминали выше в разделе «процессинговых добавок».
Представьте линию по упаковке печенья в гибкий полимерный контейнер - на старте на конвейерную ленту выпадает лоток, в него заботливые и уставшие женщины ( или умные машины и механизмы) укладывают продукты - и далее все это уезжает на запайку. Без жирных кислот, амидов жирных кислот или восков - контейнеры просто не выпадут.
Если же вы изобретаете двигатель внутреннего сгорания, в шестеренки стоит ввести фторполимеры.
II. Добавки, работающие с физико-механическими свойствами и горючестью:
1.Нуклеаторы - помогают повысить жесткость, ударную вязкость, прозрачность, снизить усадку - за счет того, что эти добавки ускоряют появление зародышей кристаллов и модифицируют кристалличность. Пожалуй, чтобы вас не путать, признаюсь, что нуклеаторы преимущественно применяются именно для регулировки оптических свойств полипропилена.
В качестве нуклеаторов используют бензоат натрия, тальк, бензойная кислота, производные дибензилиденсорбитола.
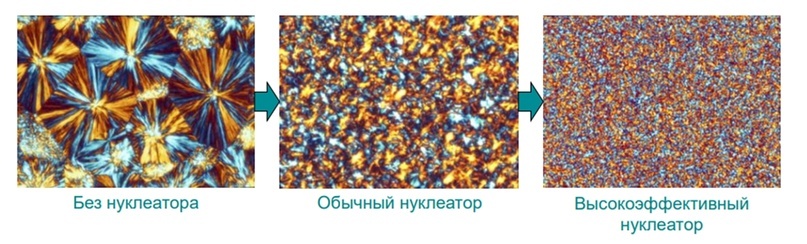
2.Модификаторы ударной вязкости, пластификаторы различной структуры. Это могут быть термопластичные эластомеры (POE), или всеми любимый бюджетный SEBS, который ко всему прочему отлично наполняется маслом - которые обладают свойствами каучука, или более сложные «ядерные» структуры, в которых стирол-бутадиеновый центр окружен ПММА (core-shell) - и эти шарики введены в компаунд.
Последние - это чудеса технологической мысли. Мы как-то встречались с подобным пластификатором ПВХ, когда пытались идентифицировать состав образца для нашего заказчика, и знаете, давненько я не слышала, как скрипят мозги исследователей, но в этот раз посчастливилось услышать.
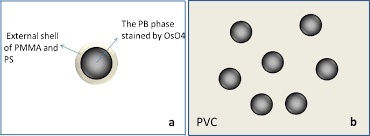
3.Третья большая подгруппа - антипирены. Здесь ваша покорная слуга должна признать, что познания ее ограничены парой глав учебника для студентов-химиков, поэтому воспользовавшись тем, что статья подходит к концу, вы уже утомились, сокращу изложение до нескольких тезисов.
Технологи делят антипирены на 3 подгруппы:
1) галоген-содержащие - и с большой долей вероятности это будет именно декабромдифенилоксид (соотношение цены/качества) - который вводится в компаунд вместе с синергистом, то есть компонентом, который усиливает действие антипирена. В нашем с вами случаем это трехокись сурьмы.
Если вы откроете справочник, то увидите, что для того, чтобы материал стал считаться самозатухающим, концентрация брома в нем должна составлять около 20%. Казалось бы, зачем нам сурьма? Бахнул в компаунд побольше этих радостных молекул, и дело с концом.
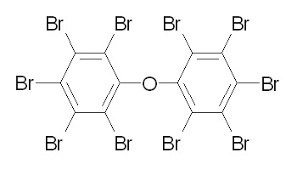
Но не все так просто: большая концентрация галогенов ускоряет деструкцию полимера, приводит к образованию пор, и выделению низколетучих компонентов - так что добавление окиси позволяет значительно снизить % ввода галоген-содержащего компонента без потери эффективности. Общий процент ввода такого наполнителя 15-30%.
Ощутимые недостатки этой добавки - экология и коррозионное воздействие на оборудование.
2) Гидроксиды металлов: они деструктируют при температуре 180-230С с выделением воды, поэтому по сути просто приводят к затуханию.
Недорого и вполне удобно - скажете вы. И будете правы. Безгалогенка набирает популярность, но имеет и очень внушительный «нюанс»: чтобы увидеть сколько-нибудь ощутимый эффект, нужно не менее 30% гидроксида в составе компаунда, чтобы добиться ПВ-0 - 70%. Вы же понимаете, на сколько «уплывут» тогда физмехи? От свойств исходного полимера не останется и следа.
Поэтому обычно производители ограничиваются 30-50%. И даже это - много.
3) Фосфорсодержащие антипирены (часто применяются в смеси с меламином и добавками, содержащими аммонийные фрагменты) - здорово, быстро, безопасно. Дорого.
III. Добавки, меняющие структуру полимера
или сшивающие агенты.
Действительно, свойства сшитого материала часто разительно отличаются от несшитого. И чаще всего, говоря о сшитых материалах, мы подразумеваем полиэтилен - Pex-A и Pex-B нашли применение в трубах для систем отопления ввиду их высокой термической стабильности, прочности, и низкого коэффициента теплового расширения. Pex-C - в производстве электротехнических изделий и муфт.
Сейчас я обязательно расшифрую эти названия:
Пероксидная сшивка тип - А - сшивка пероксидами (часто это перекись дикумила) происходит в условиях высоких температур и давления: в результате образуются прочные связи по всему объему материала - сшитый таким образом ПЭ будет иметь достаточную прочность в независимости от его толщины.
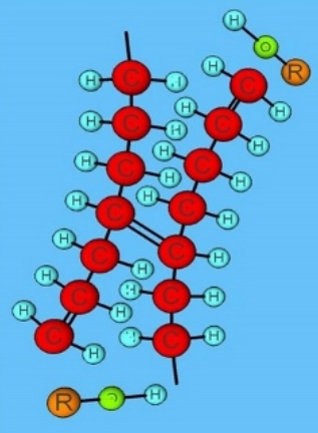
Силанольная сшивка - тип B:
При нагревании связи винильной группы разрушаются, превращая молекулы в активные радикалы. Эти радикалы замещают атом водорода в макромолекулах полиэтилена.
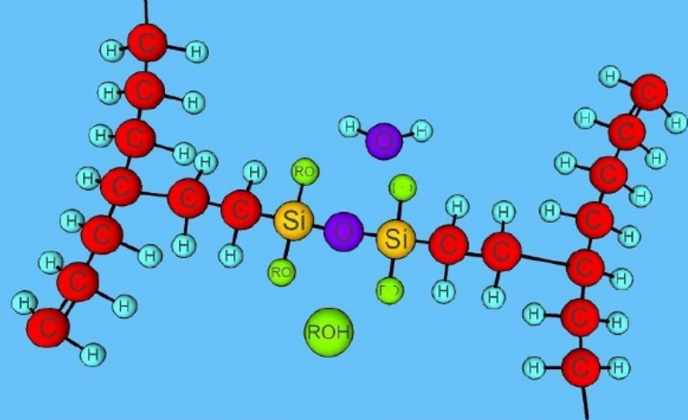
Полиэтилен, в который введена силанольная добавка, обрабатывают водой либо водяным паром: органические радикалы при этом присоединяют молекулу водорода (из воды) и образуют стабильную гидроокись (органический спирт).
Соседние радикалы полимера замыкаются через связь Si-O, формируя пространственную решётку. Вытеснение воды из PEX ускоряется при помощи оловянного катализатора. Процесс окончательной сшивки происходит уже в твёрдой стадии изделия - и в этом принципиальное отличие в технологии изготовления изделий из этого материала от Pex-A: экструдированные изделия буквально «варят».
Есть еще радиационная сшивка - тип С. Но в этом случае сшивка происходит с помощью циклического ускорителя электронов, никакие добавки в материал не вводятся, поэтому эту историю оставим для следующих статей.
В завершении хочется обратить ваше внимание на то, что помимо всех вышеперечисленных преимуществ разного рода добавок, при составлении рецептуры нужно не забывать о том, что добавки могут влиять не только на материал, но и друг на друга: могут как усиливать действие «соседа по парте», так и снижать его эффективность. Могут вообще прореагировать друг с другом с выделением неожиданных для технолога-разработчика продуктов, могут внезапно вспениться, со временем мигрировать на поверхность или вдруг начать пахнуть носками вашего соседа по общежитию.
Чтобы этого не произошло, обращайтесь к профессионалам, и читайте наши статьи:)
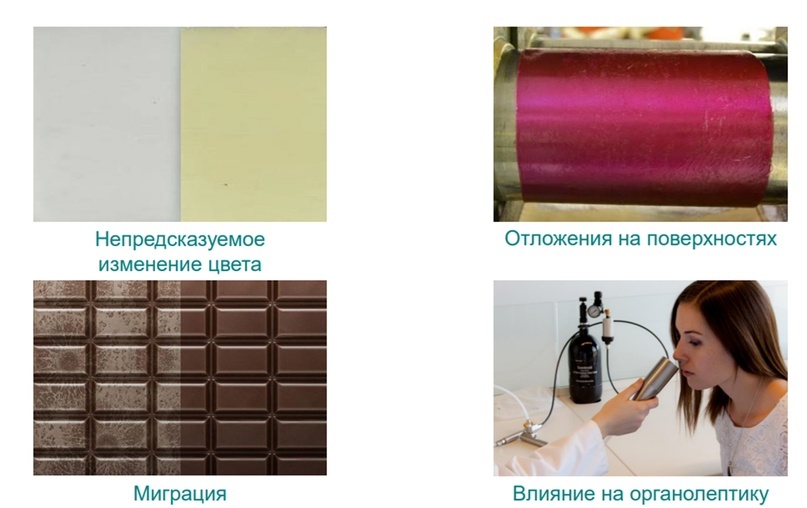